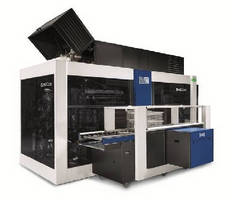
With its EcoCCore system now superseding the previous 81C/P equipment series, Dürr Ecoclean is setting new standards in solvent-based part cleaning. This is due, on the one hand, to a one-third increase in product throughput and load weight which yields a marked reduction of per-unit cleaning cost. On the other hand, the new machines are equipped for improved cleaning performance, superior process reliability and significant energy savings. Designed to use non-halogenated hydrocarbons and modified alcohols, the EcoCCore also boasts superior ease of operation, less space demand and a translucent design.
Whether in machining or metal forming, aerospace technology, medical equipment manufacture or other industries – wherever grease-free surfaces must be obtained, solvents are the part-cleaning medium of first choice. Users' priority lists are topped by process reliability, cost and energy efficiency, high speed, availability, short delivery times and eco-compatibility. Accordingly, when Dürr Ecoclean set about developing the innovative EcoCCore, the focus was placed on these factors. The new system is characterized by an extensive standard equipment level including, e.g. two flood tanks, heat recovery, and full-flow plus bypass filtration capabilities. Switching from non-halogenated hydrocarbons to modified alcohols and back is particularly easy, so the EcoCCore – which operates under full vacuum conditions – is a forward-looking solution which also addresses changing future needs. In combination with appropriate solvents, this system can even remove chlorinated oils from parts surfaces.
High throughput for reduced cost per unit
The work chamber is designed to hold cleaning tanks measuring up to 670 x 480 x 400 mm, thereby offering one-third more loading volume than the 81C/P predecessor system. Throughput can thus be doubled, depending on the basket size. The maximum load weight capacity has likewise been increased by more than 30 percent to 200 kg. With a cycle time of less than 8 minutes this provides a significant reduction in per-unit cleaning cost.
Innovative technology for optimized cleaning quality
A major step towards improved cleaning quality lies in the new preliminary steam degreasing process. Here the oil-containing distillate is not passed into the flood tank as usual but is directed straight into the distilling system. This minimizes oil deposits in the flood tank and an undesirable oil enrichment of the solvent. The result is an enhanced degreasing performance that will be found particularly beneficial with parts to be coated or laser-welded after cleaning. In addition, the preliminary steam degreasing step offers advantages under elevated oil drag-in conditions or when a second flood tank is used for a preservation treatment. This is made possible by an almost doubled distilling capacity.
Another innovation boosting cleaning performance is the capability to use ultrasound and filtration simultaneously. Here particels are discharged throughout this process cycle, opposed to conventional systems whereby they can settle at the bottom of the work chamber before being filtered. To this end the EcoCCore pumps are equipped with variable-frequency drive units and control the volumetric flow rate in such a manner that the ultrasonic system can exert its effect. This efficient and flexible combined filtration system ensures an effective discharge of particles. Moreover, the unit comes with a frequency-controlled rotary drive for turning and high-accuracy positioning of parts. A "gentle" operating mode prevents sensitive parts from getting dropped or displaced during start-up or handling operations.
Internal heating elements have been removed from the stainless steel flood tanks. Here, the design eliminates the potential of particle trap points or chip accumulation thereby reducing any re-contamination of parts.
High process reliability thanks to ease of operation
Operating the EcoCCore machine is made simple, fast and safe by the new 7" color display based on self-explanatory pictographs. Thus, for instance, a temperature needs to be preset only for the first flood tank; a matching setting for the second tank is then selected automatically. Process tracking and maintenance, too, are rendered intuitive and more convenient by the integrated part visualization system. An optional full visualization capability can be integrated above the control panel.
Efficient in every respect
In developing this system, Dürr Ecoclean's engineers paid particular attention to high efficiency and ease of maintenance. Thus, for instance, both flood tanks are heated entirely with thermal energy recovered from the distilling circuit. The heat input from the distilling system can be adjusted as needed in multiple stages. As a result, energy is saved on the one hand while on the other, a high throughput will be guaranteed even with high oil drag-in rates. For the discharge of oil, a new process based on jacket heating which is fully decoupled from the distilling system ensures optimized, gentle oil evaporation. As a result, a much broader range of oil grades can be removed in safe and reliable manner. Moreover, oil encrustation requiring costly and time-consuming cleaning is avoided. Cost savings are also achievable by the new level control system which effectively prevents a carryover of preserving medium, thereby reducing its consumption. Switching from cleaning to preserving mode can be made simply by the push of a button on the operator panel.
Smart and attractive machine design
The design of this equipment, honoured with the 2013 Design Award of the state of Baden-Wuerttemberg, is striking not least due to the integral loading system and its all-round enclosure made of safety glass. Moreover, the universal EcoCCore machine requires around 5 percent less floor space than its 81C/P predecessor. A further benefit is that its top height can be reduced to only 2.25 m by removing just a few components where access to the installation area is difficult. This capability can also cut freight charges, e.g., for shipment to Asia, the U.S. or South America. For these destinations it is also possible to ship the core unit to the nearest Dürr Ecoclean site at low cost and to complete its assembly there. |